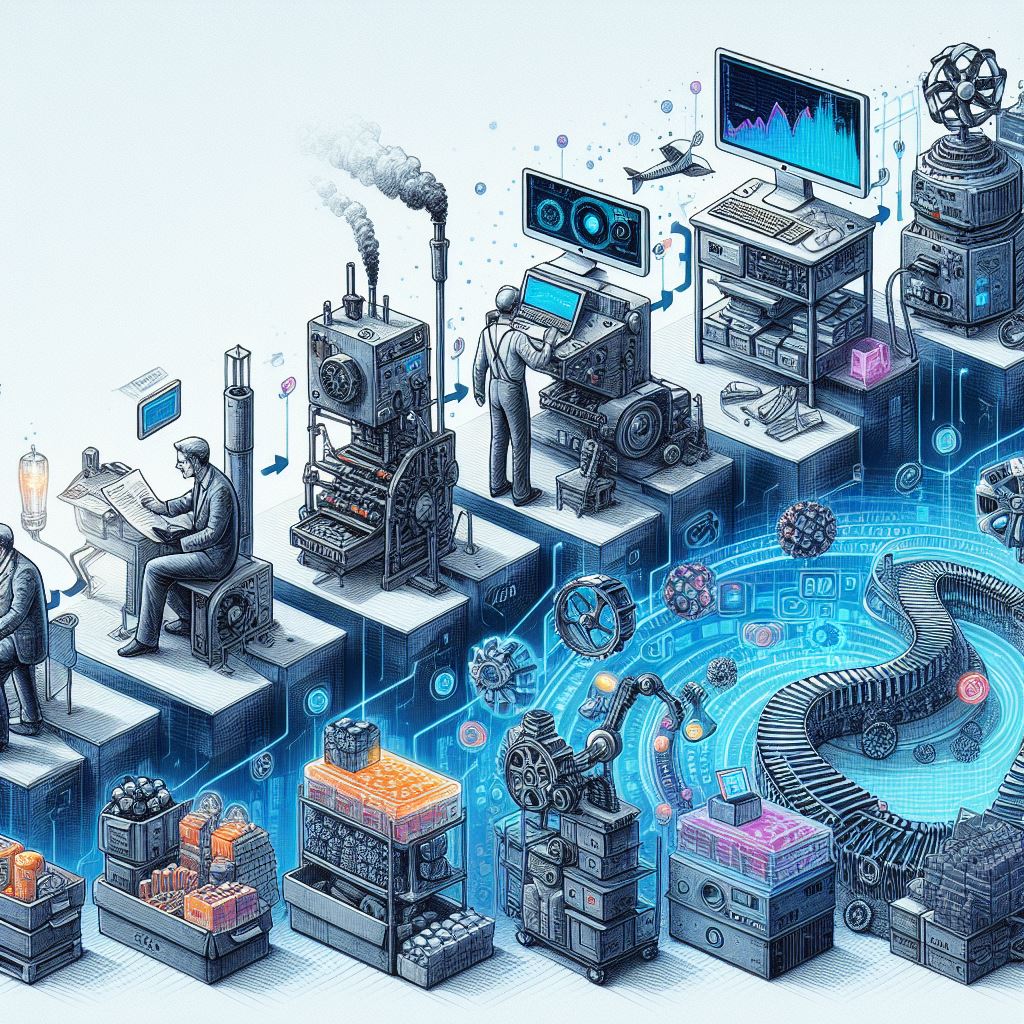
В постоянно меняющемся ландшафте производства способность контролировать и эффективно управлять операциями всегда имела решающее значение. По мере того, как рыночные условия усложняются, а доступность квалифицированной рабочей силы снижается, предприятия вынуждены внедрять инновации и адаптироваться. Переход от прошлых практик к современным стратегиям — это не просто технологический прогресс, это вопрос выживания.
Прошлое: Ручной сбор и анализ данных
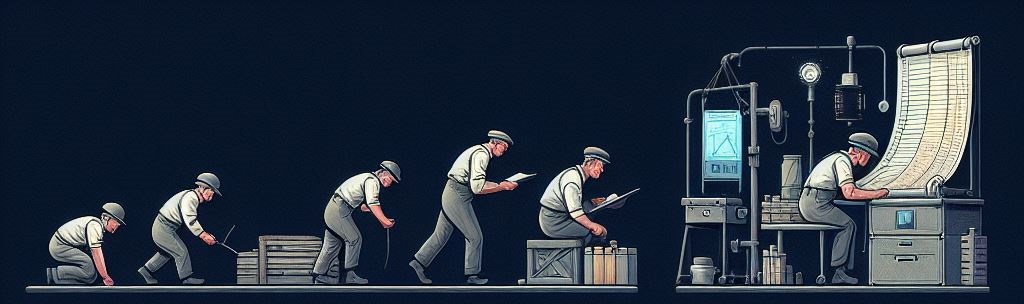
На ранних этапах развития промышленного производства мониторинг производства в значительной степени зависел от ручных процессов. Операторы регистрировали производительность оборудования и оперативные данные на бумаге, что приводило к задержке ответов и неточностям в данных.
Унаследованные системы, такие как MES и ERP, хотя и обеспечивали структурированный подход к организации данных, были жесткими и негибкими, что часто приводило к примитивному, ориентированному на материалы взгляду на операции. Такой подход, основанный на ручном управлении процессами, был неэффективным, особенно в условиях растущего кризиса рабочей силы.
Многие предприятия продолжают работать в рамках этого традиционного производственного мышления. В результате они практически не имеют представления о текущем состоянии операций и обладают скудным набором данных для принятия решений.
Если сотрудник предприятия не имеет базовой информации о состоянии производства, как он может принимать быстрые и эффективные решения?
Настоящее: Базовые решения для мониторинга
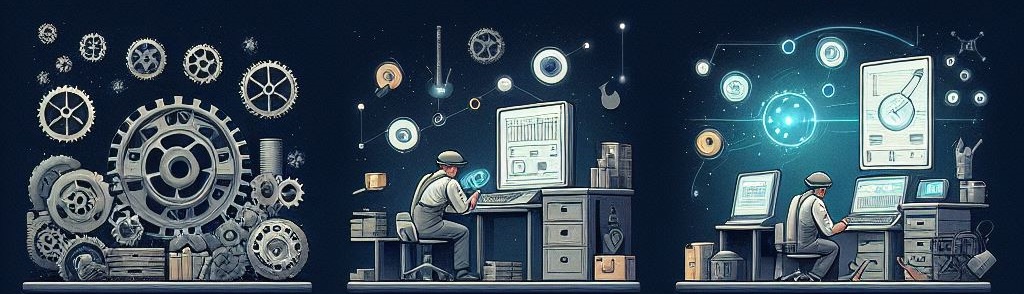
В настоящее время многие предприятия оказались в ловушке между прошлым и будущим. Хотя некоторые из них используют базовые цифровые инструменты мониторинга, эти системы часто требуют ручного ввода данных и предоставляют ограниченное представление о производстве.
Это вынуждает операторов выполнять большую часть ручной работы на переднем крае, ежедневно собирая и вводя данные. Кроме того, это, как правило, приводит к проблемам на заднем плане, когда необходимо собрать и проанализировать данные.
Предприятиям нужны не только основные производственные данные. Им нужны глубокие сведения о производительности и состоянии оборудования. Кроме того, эти данные должны быть представлены в контексте бизнеса и операций.
«Базовые» решения для мониторинга поддерживают основные сценарии использования, но не предлагают цифровую инфраструктуру, способную видоизменить и продвинуть бизнес.
Будущее: Решения следующего поколения для мониторинга производства
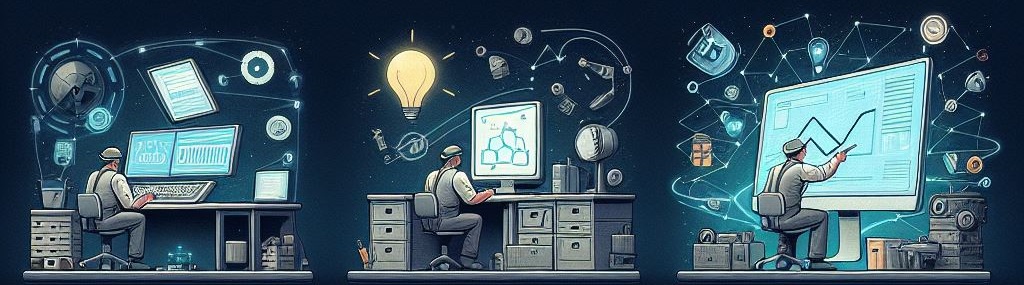
В будущем мониторинг производства должен претерпеть трансформацию: от базового сбора данных до получения действенных выводов, поддерживающих все уровни производства. Эта эволюция представляет собой значительный скачок в том, как предприятия управляют и повышают эффективность производства. И она уже началась.
Сложная аналитика и использование данных
Следующая эра промышленной аналитики будет определяться решениями, позволяющими извлекать максимальную ценность из машинных данных. В то время как в настоящее время рынок предлагает множество базовых решений — в основном для сбора ограниченного количества данных с оборудования, — на верхнем уровне рынка наблюдается растущая дифференциация. Передовые платформы производственной аналитики возглавляют этот процесс. Они предлагают комплексную цепочку создания стоимости данных, включающую в себя глубокий сбор машинных данных, стандартизацию, контекстуализацию и глубокую аналитику. В данные вплетается ключевой бизнес и операционный контекст, что позволяет пользователям по-настоящему понять производительность каждого станка, человека, рабочего места и детали.
Действенные идеи: Ценность за пределами самих данных
Будущее за тем, чтобы не просто собирать данные, а преобразовывать их в действенные идеи. Этот сдвиг крайне важен, поскольку одних только необработанных данных недостаточно для принятия эффективных решений. Очень важна контекстуализация этих данных: понимание того, когда и как работает техника, кто ее эксплуатирует и в каких конкретных условиях. Эта информация имеет решающее значение для преодоления разрыва между информационными и операционными технологиями, обеспечивая не только сбор данных, но и их эффективную интеграцию в операционные и бизнес-процессы.
Предиктивная и предписывающая аналитика
Аммолит находится в авангарде этой эволюции, превращая производственные данные в критически важные сведения на различных операционных уровнях. В настоящее время наблюдается тенденция к развитию предиктивной и предписывающей аналитики, когда системы не только сообщают о том, что произошло, но и предсказывают будущие результаты и предписывают действия по улучшению ситуации. Такой подход позволяет опережать проблемы до их возникновения и оптимизировать работу в режиме реального времени.
Межсистемная интеграция и совместимость
Несмотря на сохранение ERP и других корпоративных систем, наблюдается заметная тенденция к распространению специализированных программных решений для отдельных производственных функций, таких как техническое обслуживание и ремонты, качество, складской учет и ценообразование. Эти специализированные системы предоставляют возможности, значительно превосходящие те, которые могут обеспечить обобщенные системы управления. Цель — создать экосистему подключенного предприятия, в которой эти специализированные решения будут работать слаженно, поддерживаемые бесшовными вертикальными и горизонтальными интеграциями. Такие решения, как Аммолит, с их обширными готовыми интеграциями и открытым кодом, играют ключевую роль в повышении эффективности и результативности этих интеграций. Способность обеспечить двунаправленный поток данных между системами, особенно между ERP и цеховыми системами, является основополагающим фактором для реализации всего потенциала подключенного предприятия.
Получение знаний и ответов с помощью данных
Переход от ручного ввода к подключенным решениям, управляемым машинами, отражает более широкие преобразования в производстве. Будущее за открытием производственных данных на уровне цеха, что позволит использовать их для создания технологических стеков и связанных с ними процессов. По мере того, как предприятия будут осуществлять этот переход, внедрение взаимосвязанных интеллектуальных решений для мониторинга будет иметь решающее значение для оптимизации операций и поддержания конкурентоспособности.